Visual Inspection
Visual inspection guarantees high casting quality. In our foundry, all procedures are carried out completely for investment castings’ flawless surfaces. Any castings with defects such as shrinkage cavities, air holes, sand holes, scales, and cracks are picked out and not delivered to our customers.
All the inspection findings are recorded and kept on file in order to track all the goods produced by our foundry.

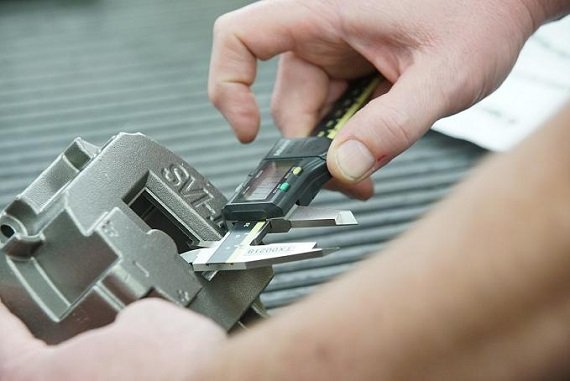
Dimensional Inspection
The typical dimensional inspection techniques applied at our foundry are the following:
- Measuring tools – A quick and easy technique to check the dimensions and tolerances are by hand. Some of the tools we used are depth indicators, vernier calipers, dial indicators, etc.
- Testing gauge – When measuring tools cannot directly evaluate the dimensions, a testing gauge is used.
- CMM – the most accurate method of measuring casting products.
Chemical Composition Inspection
Various metal alloys are used to create investment casting pieces. Each materials have their own unique properties. Any errors in the composition of the elements could cause our clients a lot of trouble. Therefore, we must ascertain the chemical composition of materials.
To perform material testing, we used spectrographic instrument. This equipment will enable us to determine whether the material composition has altered as a result of casting or heat treatment. Additionally, the outcomes of each batch test will be noted in our laboratory area for future reference.
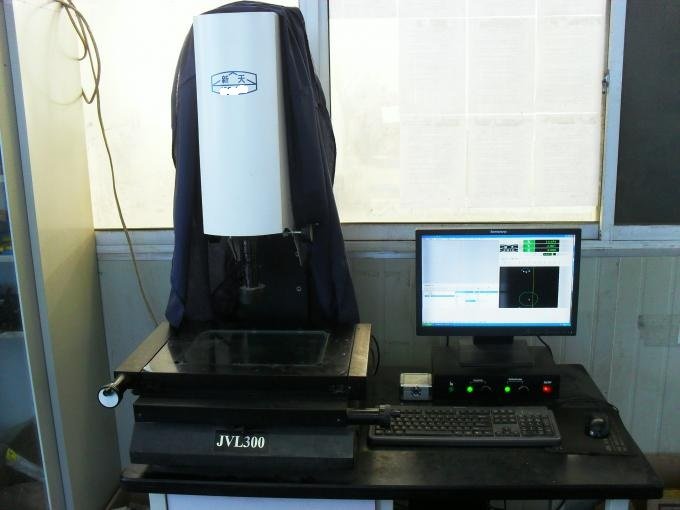

Mechanical Properties Testing
Product quality is verified through mechanical testing. Testing shows that the qualities meet the required mechanical specifications. To verify correct casting quality, testing of the below mechanical qualities can be done.
- Hardness testing – When investment castings must meet a hardness requirement, they are tested for hardness. Results of hardness tests are often displayed in HRC or HB.
- Tensile testing – a destructive test method that determines a product’s maximum tensile strength as well as its elongation, yield strength, and reduction area rate.
NDT Testing
We have the capacity to evaluate the quality of an investment casting part without destroying it using NDT (Non-Destructive Testing). Here are some of the most popular NTD testing techniques:
- Dye Penetrant Inspection
- Magnetic Particle Inspection
- X-ray Inspection
- Ultrasonic Testing
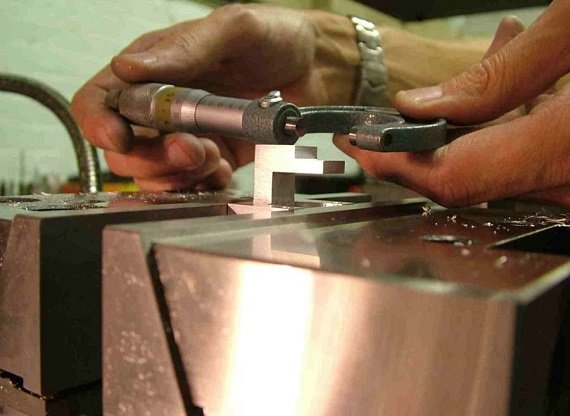