Investment casting and machining are common manufacturing process in most industries today. You can fabricate both metals and plastic to make suitable parts of your choice.
In this guide, are going to compare these two processes to help you choose the best process for your fabrication needs. Let’s dive right in.
What is Investment Casting?
Investment casting is an old processing method also referred to as lost-wax casting. The procedure has undergone modification over the years to make it more compatible with modern technology and applications.
Investment casting involves forming a wax replica of the parts needed. The obtained model is then covered with a ceramic mold the wax is melted out and replaced with molten metal. After cooling the resulting product is removed from the mold. It gave a more refined finish.
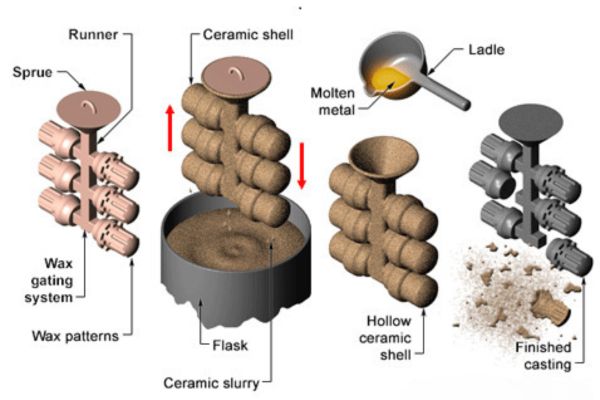
What is Machining?
Machining is a fairly recent modern fabrication process that uses automated tools to design desired parts. The final product is obtained by chipping off pieces from the original metal until it obtains the desired shape.
Pre-programmed software is used to control the machine tools that are used to carry out this process. Different configurations result in a quick process that can form a variety of parts using the machine
Comparing Investment Casting to Machining Processes
Advantages of Investment Casting
- Investment casting provides a smooth finishing of the surface and does not require extra steps to smoothen out the end product.
- Ceramic molds can be fashioned to accommodate more intricate geometrical designs. Investment casting is therefore suitable for fabricating more intricate designs.
- A wide range of raw materials including bronze, stainless steel, brass, and aluminum can be molded using investment casting.
- Material wastage is reduced with this method of casting. It utilizes molten material and does not require polishing ensuring that no materials are wasted.
Advantages of Machining Processes
- The lead time is drastically reduced as the entire process is carried out using machines that are already programmed.
- A variety of raw materials including composites, plastic, and metal can be molded using the machining process.
- Machining processes have increased accuracy and precision making it ideal for some complicated designs.
Limitations of Investment Casting
- The lead time for investment casting is slightly higher as it requires time to form the ceramic mold before casting the metal
- Investment casting is mostly used to form metallic part
- It has increased production costs as it requires the formation of wax models and ceramic molds for the different designs.
Limitations of Machining
- Parts produced through the machining process require finishing touches to smoothen the surfaces.
- Machining is not suitable for highly complex designs
- The process leads to a lot of wastage as it involves chipping away metal or plastic from a bigger portion.
· Accuracy
While machining produces pretty accurate designs and dimensions, finish touches are still required to smoothen and shave down minor irregularities. The ceramic mold used in investment casting is usually very precise and therefore the finished products are more accurate.
· Cost of Production
The initial cost of purchasing the Machining equipment is fairly higher than the tools required for investment casting. However, the machining system can be used for a long period to fashion different designs making adjustments only to the software parameters.
Investment casting requires the molding of new wax models and ceramic molds for each different design. Operational costs of the investment casting are therefore higher than those of machining.
· Speed of Fabrication/Production
Machining processes have a shorter lead time. The process is automated and therefore fairly faster than investment casting. However, despite the shorter production time the produced parts still require finishing which is not the case in investment casting
· Materials each Process Handles
The investment casting can be used to produce parts from a metal. A wide range of raw materials including bronze, stainless steel, brass, and aluminum can be molded using investment casting.
With machines, more diverse types of materials can be used. A variety of raw materials including composites, plastic, and metal can be molded using the machining process.
· How the Two Processes Work
Investment Casting Process
The first step in investment casting is to create the pattern. Specifications from a finished product are used to create the model. Using a metal injection die the model is formed from wax.
The next step involves mounting the wax molds and forming a tree. This is done by combining the molds created. If similar designs are smaller in size, they can be formed at once by creating one big mold.
After joining the wax models, the model is then dipped into a ceramic slurry. Sand stucco is then poured onto it and then it is set aside to dry.
After it has sufficiently hardened the next step is to empty the mold. Wax removal is done using a steam autoclave which melts away all the wax. Heating also helps in further hardening the ceramic mold.
At this stage we preheat the ceramic mold. Preheating ensure the mold temperature matches that of the molten metal. Ideally, this is a safety measure that protects the mold from drastic change in temperature.
Next, you will pour the molten metal then allow it to cool to make lost wax cast part.
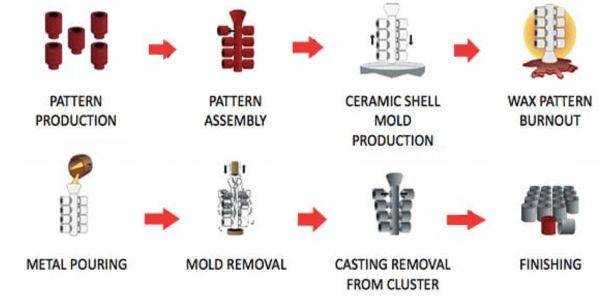
Machining Process
The machining process involves two main processes. The first process is referred to as turning. Turning is carried out by a tool known as a lathe.
A lathe is responsible for spinning the materials around exposing all the parts to cutting tools. Cutting tools are programmed to work along two motion axes, obtaining the desired cuts across the length and width of the material. The turning process can be done both internally and externally as desired. For pieces that require opening or holes of a drill bit can be separately be incorporated separately.
Milling is the next step in this process. Rotating cutting tools are used to shave off the bits of metal to obtain the desired shape. The milling process also includes a moving table or slab that moves the piece to properly position it.
Different types of millers are used to design different types of materials. Tools such as grinders, planners, and saw broaches are used to further shape and smoothen the piece into the desired finish product.
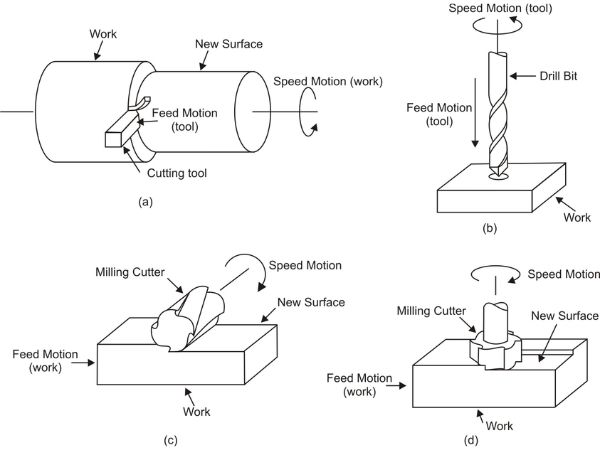
Factors to Consider when Choosing Investment Casting vs. Machining
Several factors should be considered when selecting the best fabrication method. These factors include
- Raw materials; Machining processes can be used to form parts from composites, plastics, and metal whereas investment casting can be used for forming parts from different types of metal.
- Lead time; Investment casting requires more time compared to machining to fabricate parts. However, the machine requires more time for finishing surfaces.
- Cost operation: Machining tools only requires a high initial cost for purchasing the tool but does not cost a lot to operate. Investment casting has a lower cost of purchase but higher operational costs.
- The intricacy of the design: With investment casting it is easier to produce more complex and accurate designs. Machining cannot handle more complex geometrical shapes.
- Surface finish: Investment casting produces a smoother finish of the final product
Conclusion
Before choosing a fabrication method you should take factors such as the material being used and the overall cost of production as well as the complexity of the designs in question in mind. Whether it is investment casting or machining select a method that will best accommodate your needs.