Hardness Testing
Hardness testing is used to determine the hardness and properties of the casting metal. The results of the hardness of various types of metal alloys can vary such as stainless steel, aluminum, etc. After the casting process, cleaning the part, and value-added services, Ucasting conducted a hardness test to improve the stability and wear resistance of casting products.
Hardness Testing Advantages
- Determine the material’s ductility, strength, and wear resistance easily
- Ensure accuracy even for larger samples
- Non-destructive test
- Quick and affordable process
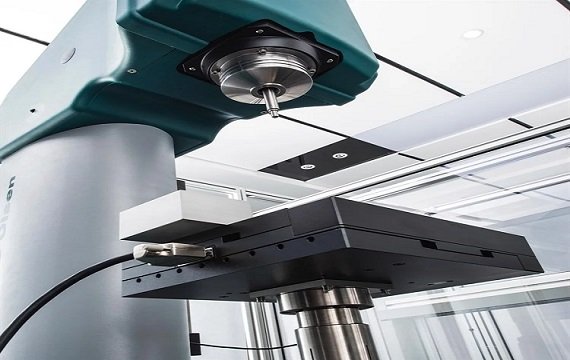
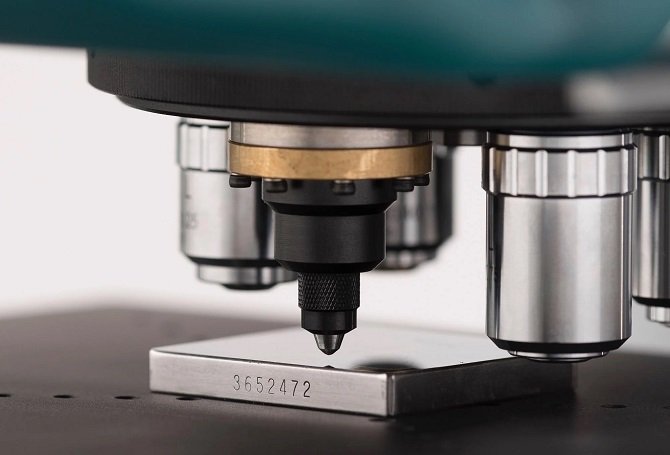
Wide Range of Hardness Testing Techniques
We perform various hardness testing techniques using advanced tools and testers. Ucasting offers the following techniques for hardness analysis:
- Brinell Hardness – Uses a spherical penetrating body hardness tester. All types of annealed and tempered steels, non-ferrous alloys, and cast iron are eligible for the Brinell hardness test. This process is not appropriate for samples that are excessively hard, too small, too thin, or whose surface cannot have a significant indentation. Brinell hardness is measured between 8 and 650HBW.
- Rockwell Hardness – We utilize the Rockwell hardness test when the sample is too small or the Brinell hardness (HB) is higher than 450. This test uses a penetrating body used shaped like a bullet or a cone. Using a diamond or ball indenter, the apparatus gives the casting a preliminary test force. This stage’s goal is to penetrate the metal’s surface. And lessen the influence of the surface finish on the outcome.
- Vickers Hardness – We used a weighty diamond indenter to force into the part. The depression caused on a polished surface is measured under a microscope.
If you require hardness testing for investment casting for your next project, you can trust Ucasting company. For more information, please contact us immediately.